The Impact of Well-Designed Weighing Processes On Product Quality
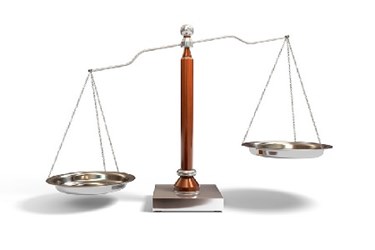
By Kevin Hill, Technical Specialist, Quality Scales Unlimited
Companies involved in the production of pharmaceutical products are well aware of the importance of consistency and accuracy in manufacturing processes. Batches that fail quality inspections waste time, labor, effort, and resources. This further leads to a loss in profits and market reputation, as well as compromises human health and safety.
Since pharmaceutical goods need to meet quality and safety requirements, every stage of the production process counts, including weighing processes that are designed to improve efficiency and accuracy. This is especially important since inaccurate weighments can negatively impact the potency of the final product through inconsistent blends/ingredients.
How Does Designing An Effective Weighing Process Work?
Also known as QbD (Quality by Design), this risk-based method involves identifying potential errors at every stage of the manufacturing process to prevent bad batches of goods. It’s a system of assessing risks and monitoring process parameters and quality-building material attributes that can be used to ensure medications and other finished products are safe and effectual.
Widely used in the food and pharmaceutical sectors, QbD has received firm support from the FDA and other regulatory authorities. This is mainly because the concept approaches manufacturing with a focus on consumer safety, and comprehensive QbD models should include batching, formulating, filling, and other weighing processes that affect final product quality for sensitive goods.
When you’re applying QbD principles to weighing processes, there are a few of the factors you should consider:
- Picking The Correct Equipment
The most essential step is to select high-quality weighing instruments that will minimize any chance of error, ensure adherence to critical industry standards, improve accuracy and reliability, as well as allow for real-time adjustments to manufacturing tolerance deviations.
You should make your selections based on the requirements of your industry, as well as the tolerance and risk analysis benchmarks, since narrower tolerance levels lead to higher requirements for qualified weighing equipment. There is a wide range of customized options available for various production stages, e.g.:
- Batching and filling stages require quick and accurate transfers of results between controller and I/O (input/output) devices
- The formulation stage requires quantities of different material to be measured in the correct amounts to guarantee exact formulations
- At the inspection stage, metal detection, X-ray, check weighing and in-process control systems help products meet regulatory and quality requirements
The weighing equipment you use will also be an essential part of the lifecycle of the manufacturing process since these instruments can work as material ID points and monitoring devices, often including extra features like information tracking or recording (for weight, raw materials, batch number, responsible operator, and more).
- Tracking And Minimizing Errors
There is always a measurement uncertainty factor associated with metrological equipment of any kind, so you need to be aware of the limitations of your instruments when they are in use, and why measurement uncertainty occurs:
- Scale design factors like readability, sensitivity, repeatability, non-linearity, and eccentricity affect measurement uncertainty
- Operating environment will also play a large role; uncertainties can be caused by environmental factors like temperature, dust, wind, humidity, vibrations, etc.
- They can also occur due to human error during manual measurements and mishandling, among other variables. Since many stages of pharmaceutical manufacturing involve manual use by an operator, it is essential to track and record relevant data for every batch. Automating as many processes as possible also helps to eliminate human error through manual use
In the pharmaceutical sector, it’s essential to ensure this deviation is small enough to have no impact on quality. Smaller samples will be affected more, e.g. if a scale is accurate to ± 1 gram, this represents an uncertainty of 0.01 percent of the reported weight while weighing a 1-kg sample, but a 10 percent uncertainty with a 10-gram sample.
Weighing scales and other equipment can be tested in their working environments to gauge and record any deviations through manual or automated documentation. These parameters can then be taken into consideration during the monitoring process and be adjusted for greater accuracy.
- Installation, Setup, And Calibration
As with any other precision devices that are critical to product quality, weighing equipment needs to be set up correctly and regularly calibrated to ensure accuracy and reliability. While it is important to select instruments that offer highly readable displays for results, it is equally or even more important to ensure that those readouts are correct.
A reliable scales service provider will be able to help you with every step of the process, from selecting the correct equipment for your production needs to installation, setup, and calibration services. The installation and setup of weighing instruments and systems should only be performed by experienced professionals, who can also assist with formulating a regular maintenance schedule.
According to the FDA’s GMP regulations and guidelines, as part of the scheduled maintenance activities, it is essential to ensure that measurement devices are properly calibrated and traceable to globally recognized standards for the pharmaceutical industry, like OIML and EA 10/18. Calibration needs to be performed when these instruments are in use, as well as at the purchase and installation stages.
Calibration allows for greater process accuracy since your equipment can be tested for deviations in eccentricity, linearity, and repeatability in controlled and working environments. Calibration also enables adjustments to be made to correct inaccuracies. With high-risk products and processes with narrow tolerances, the frequency of testing and calibration will need to be higher. For software, validation methods and protocols for process reproducibility and safe data management are essential for formulation or batching applications.
About the Author: Kevin Hill enjoys everything mechanical and works for Quality Scales Unlimited. He regularly blogs on various weighing industry-related blogs.