Romaco At Pharmtech 2015 In Moscow
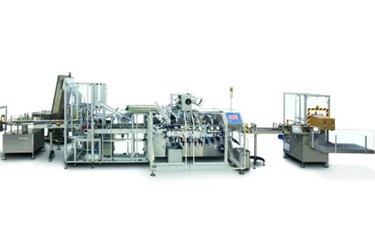
Comprehensive pharmaceutical portfolio
The Romaco exhibit at this year’s Pharmtech will comprise the Innojet, Kilian and Promatic product lines featuring an array of innovative solutions for granulation, coating, tableting, cartoning and final packaging. The synergetic effects of multiple technologies from a single supplier have clear advantages for users.
Versatile secondary and final packaging line from Romaco Promatic
At the upcoming Moscow exhibition Romaco will show its Promatic P 91 intermittent motion cartoner in line with the Promatic PAK 100 case packer for packing bottles into cartons and cases. Romaco Promatic cartoning solutions are ideally suited for a wide range of applications and provide absolute flexibility when it comes to feeding products, instruction leaflets and inserts. The cartoner’s modular design and balcony architecture are in conformity with all GMP requirements, so that no supporting structure is needed on the operator side. The easy access to the individual machine components reduces retooling and cleaning times to a minimum. Reproducible and tool-less format changes are completed in under 15 minutes. The Promatic P 91 boasts a maximum output of 100 folding cartons a minute.
Once the good packs have been positively released by the cartoner, the cartons are automatically transferred to the case packer. The Promatic PAK 100 is a semi-automatic machine which can be used to group, stack and insert folding cartons. The only manual steps are case erection and feeding. This compact machine is very easy to operate and altogether affordable. With a maximum output of five cases per minute, it is optimally adapted to human work patterns. When installed in an in-line configuration with the Promatic P 91 cartoner, the PAK 100 forms an efficient secondary and final packaging unit.
Romaco Kilian tableting technology: cool, fast & clean
The design concept for the Romaco Kilian KTP 420X tablet press was prompted by the motto “cool, fast & clean”. “Cool” stands for the reliable cooling of the process area to below 30°C. Special compression rollers, bolts and bearings reduce mechanical friction and hence bring down the temperature in the compaction area. The efficient cooling of the V-ring seals and drives likewise prevents the formation of heat. Thanks to the low process temperature, the Kilian KTP 420X is ideal for processing temperature sensitive medications such as Metformin or Ibuprofen as well as for many products with poor flow properties.
“Fast” – this high speed press is as fast as they come. It was especially developed with quick product and format changes in mind. The die-table, tablet chute and fill shoe can be swung right out for easier access to the various components. There are fewer product-contacted parts overall, so that cleaning is restricted to a minimum. The tool-less format changes also speed up retooling.
“Clean” – the optimised hygienic design ensures a strict separation between the compaction and service areas, thus preventing tablet dust from entering the machine compartment. The patented bellows protect the tablets from contamination with lubricants as they are pressed. This not only improves product quality but also makes the process more reliable. Romaco Kilian’s new generation of HMI panels featuring zoom and swipe navigation was inspired by modern smartphone technology. The Kilian KTP 420X achieves a maximum output of 360,000 tablets an hour.
Romaco Innojet VENTILUS: the lab-scale all-rounder
The laboratory-scale VENTILUS processes particles from 10 µm to 30 mm in diameter, such as powders, granulates, pellets, tablets, capsules and numerous other free-flowing bulk materials. It is the perfect granulation and coating system for pharmaceutical, food and chemical products. The machine is based on the air flow bed technology originally developed and internationally patented by Dr. h.c. Herbert Hüttlin. The homogeneous flow conditions inside the cylindrical product container enable extremely gentle intermixing of the batch. The uniform, abrasion-free circulation of the particles in the container, driven by the process air, guarantees an absolutely even coating with liquid binding and coating material. Excellent coating results are achieved, even with highly friable products or ones with a hollow structure or complex geometry. The efficient control of the process air permits up to 25% shorter drying times.
The spray liquids are applied by means of a ROTOJET, the bottom spray nozzle positioned in the centre of the container. Its circular design allows the droplet size to be exactly defined by varying the size of the spraying gap. The rotation of the spray head prevents the gap from becoming blocked, which is a great advantage if the liquid has a high solids content. The selective use of spraying and support air determines the direction of the spray jet and leads to precise, reproducible process control. The resulting formulations achieve the required release profile with between 10 and 15% less spray liquid.
On show at Pharmtech, Moscow (Russia), from November 24 to 27, 2015 (Hall 8, Booth B511).
Source: Romaco