Pharmaceutical Operations Management: Manufacturing for Competitive Advantage
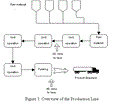
By: Pankaj Mohan, Jarka Glassey, Gary A Montague
Click here to purchase Pharmaceutical Operations Management at a discounted price!
Be sure to visit the lead-in author Pankaj Mohan in the Cyber Café at INTERPHEX2006. He will be signing copies of his book.
Excerpts
A productivity conscious organization has a distinct competitive advantage. Productivity should be viewed as an integration of knowledge, leadership and silo-less synergy. Successful productivity efforts require:
- Transformational leadership that can lead the implementation of a comprehensive vision
- An improvement infrastructure that can support the vision and implementation
- Successful adoption of the Six Sigma methodology
- A learning organization
Productivity Improvement Case Study
The operations involved in the pharmaceutical production process are: raw material storage, raw material treatment, three unit operations, packing and shipment.
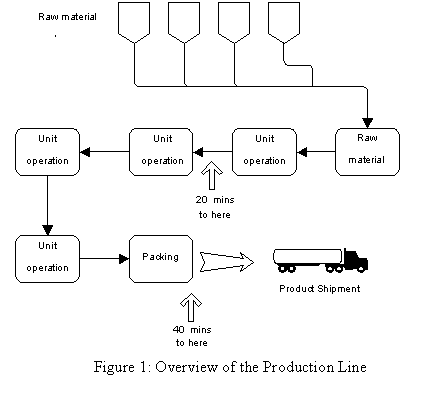
Define
An improvement opportunity was identified based on external benchmarking with input from external consultants. The quality, organizational, technological, and financial risk was minimal. A well thought out cost justification was prepared for this case study. Inevitably, some assumptions about performance enhancement will have to be made to arrive at an estimate of savings. One possibility is if the objective is to improve the performance of a large-scale manufacturing plant, an estimate of the ultimate performance could be obtained by applying the strategy to a pilot scale plant. Assuming the availability of a pilot plant, this does not overcome the necessity for engineering work and hardware and software costs. Thus while it would provide confidence in the likely applicability of the method to large scale, it would not satisfy the fundamental objective of assessing likely savings before purchasing and implementing the system. The major benefit gained by adopting this approach would be minimizing the risk of lost production, but the question of scale on system performance is a major issue. Under these circumstances the more presumptive approach of cost benefit analysis must be applied.
The strategy for cost benefit analysis can be applied to process improvements achieved through changes in operating procedures or plant equipment modifications. The emphasis in this section is on operating policy improvement through improved process control. Cost benefit analysis is possibly one of the most difficult areas to be considered in the development of a control system for process improvement. Here the term ‘control system' is used in its widest sense as referring to any technology that delivers improvement in operation.
Measure
When considering the implementation of control scheme modifications, it is essential to establish a base case against which improved operation can be assessed. This involves building a historical record of operation prior to improvements and comparing this against resulting performance. In doing so it is vital to agree on the method of quantifying performance at the outset to avoid conflict in interpretation of the future results. Historical process operating records usually provide the necessary information. The technical requirements for a particular control system improvement can generally be ascertained prior to purchase by using a combination of past experience and process tests. However, what is much more difficult is to determine how much improvement in control is possible and what the financial consequences of this improvement are.
An approach to cost benefit analysis that has been widely applied in the chemical industry to justify process control system investment, is presented by Anderson (1996) and Anderson and Brisk (1992). The basic assumption of the procedure is that improvements in control will at least halve the existing variance of the output. This is a tried and tested statistic and the extent to which it can be exceeded obviously depends upon the existing quality of control; where little attention has been paid to control it is likely to be an underestimate. On well controlled plants, this level of reduction of variance may require the implementation of some complex control schemes as described in Chapters 3 and 6. In the chemical process industries, the average improvements from implementing various levels of control have been estimated. The Table 1 uses information from Anderson (1996), and gives an indication of savings achieved through control improvements.
Click here to download the complete excerpt.
Click here to purchase Pharmaceutical Operations Management at a discounted price!
Get unlimited access to:
Enter your credentials below to log in. Not yet a member of Pharmaceutical Online? Subscribe today.