Designing HVAC systems for biosafety level requirements
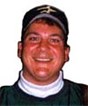
By Joseph DeLaurentis, Kinetics Biopharm
The design of HVAC systems to meet biosafety level requirements presents special challenges. The design must be closely studied and evaluated for safety, capital and operating cost, maintenance, accessibility, construction and validation schedule goals, as well as any additional client requirements. The HVAC design team must coordinate its efforts with those of the process and architectural design teams in the early conceptual and preliminary phases of a project to meet these critical factors.
This article provides general HVAC design considerations to meet biosafety levels for cleanrooms as defined in US standards and guidelines and European Community (EC) standards.
Design considerations
Terminal HEPA filtration provides all supply airflow. The HEPA filter is the last thing the air comes into contact with prior to entering the room. Some Class 100,000 (US) and Class "D" (EC) areas are designed with ductwork inline HEPA filters, with conventional laboratory air outlets ducted from the inline HEPA filters. If this design is used, then all ductwork downstream of the HEPA filters must be either anodized aluminum or stainless steel, because other materials shed and flake particles into the airstream and, therefore, the room.
Areas must be environmentally controlled, with temperatures normally between 65-72°F depending on gowning requirements. The control tolerance should be as tight as possible. However, it is important to verify temperature requirements based on the product or process application. If required only for personnel and cleanliness purposes, humidity should be maintained between 35-55% RH (if lower, static electricity becomes a problem; if higher, bacteria or mold can form). A 45% RH +10% room design condition is recommended. Individual zone trim humidifiers can provide tighter humidity control if required. Historically, some systems with many zones have maintained a +7% RH. Each system or zone must be individually evaluated. A "zone," in HVAC terms, is defined as an area controlled by the same HVAC system or separate HVAC component of the central HVAC system.
Since steam is injected directly into the airstream for humidifying purposes, clean steam is preferred for cleanliness, although it is more expensive to use than plant steam.
Notes:
1Although US guidelines allow airflow to be recirculated, it is not recommended. All airflow from biological safety cabinets must be 100% exhausted, and the exhaust air must be HEPA-filtered prior to exiting the building. All degowning areas and exit airlocks should be designed for 100% exhaust, which includes all supply and infiltration airflow.
2All airflow must be HEPA-filtered whether exhausting or recirculating. Double inline HEPA filters in series have also been implemented in certain designs.
3The term "negative pressure" does not mean that the cleanroom is below atmospheric pressure. Rather, it means it is negative relative to surrounding areas, which must have the same cleanliness classification or higher when drawing airflow from other areas. Therefore, "dirty" or gray interstitial areas above the ceiling must be airtight. The pressure differential should be a minimum of 0.05" W.G. with respect to non-biosafety areas, but a 0.06" W.G. design (not necessarily documentation) is recommended to provide a safety control tolerance (refer to Note 4 below).
4It is highly recommended that equipment serving these specific areas be segregated from the rest of the facility. For example, although these rooms are segregated, a secondary barrier should be provided for equipment located in the "dirty" or gray areas to segregate it from the rest of the facility. This area should be designed negative with respect to atmosphere, possibly above the "pressurized" contained area. Decontamination, cleaning, and maintenance of this equipment are segregated, providing an additional safety barrier to the rest of the facility.
5Additional controls/interlocks are also recommended/required. The design team must ensure that these areas are maintained under a negative room air pressure (with respect to adjacent areas) at all times and should evaluate each HVAC system serving these areas in addition to the systems serving the areas surrounding the containment areas.
6Certain areas entering (not exiting) these biosafety levels (e.g., gowning rooms) may be designed for positive airflow out to non-biosafety areas, while pressurizing airflow into the biosafety area.
Joseph DeLaurentis has more than 21 years of engineering and design experience, including 16 years in the biopharmaceutical and microelectronics industries. His responsibilities have encompassed all design phases and tasks from conceptual design through construction turnover to owner. Joe attended Drexel University.
For more information: Joseph N. DeLaurentis, Lead Building Mechanical Systems Engineer, Kinetics Biopharm Division, 7 Penn Center, 1635 Market St., Philadelphia, PA 19103. Tel: 215-656-2544. Fax: 215.561.4444. Email: jdelaurentis@kineticsgroup.com.