Boehringer Ingelheim Revolutionizes Filling Line Flexibility
By Trisha Gladd, Editor, Life Science Connect
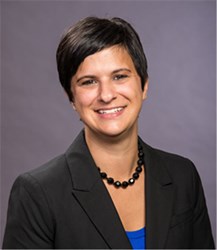
Every pharmaceutical manufacturer has one ultimate goal in mind—to deliver a safe and effective drug to market quickly at the lowest cost possible. This desire is what drives many companies to constantly re-examine their processes and technology to ensure they’re using the best methods to achieve this outcome. At Boehringer Ingelheim, experts wanted to design a new filling line that was smaller than the traditional large isolator filling line yet still maintained a lot of the aspects of traditional filling lines—the goal being to not only maintain safety and quality while speeding up production but also to reduce costs.
Breaking The Mold: Vial And Syringe Changeover On One Line
Brian Greven, Senior Associate Director at Boehringer Ingelheim, says BI wanted to build a state-of-the-art filling line, but first they needed to define what that meant. “We determined what we were going to do from a design standpoint and we decided that a state-of-the-art filling would have all components ready to use,” he explains. “Now, because we had the traditional types of utilities that are built into filling facilities but with ready to use, we were able to eliminate the items required for vial washing or depyrogenation of the vials.”
Using standard filling machines from Bausch and Stroebel, the BI isolator filling line allows for the same isolator to be used for syringes and vials with quick and easy change out. “BI was able to place the standard Bausch and Stroebel filling machines onto stainless steel L-flanges, and these L-flanges can be wheeled in and out of the isolator, so you can have one isolator for two filling lines,” explains Greven.
He adds that, to his knowledge, a filling line that allows changeover from vial to syringe isn’t currently available, because the format parts that would need to be changed are prohibitively expensive in terms of timeline. However, due to the fact that the BI filling line allows for the use of ready-to-use materials and disposables, the investment costs for clean-in-place (CIP) skids and steam-in-place (SIP) skids are reduced significantly. “The filling line is a very localized space that allows the operators to use gloved hands to complete filling operations in the isolator,” adds Greven. “We were able to reduce the cost of investment by leveraging the existing technology for ready-to-use components, and because the utility demand was so small, we're able to tie into our existing utilities.”
Greven says the filling line has a Class A ISO-100 classification, eliminates the need to have operators in the area, and offers a throughput that could meet both clinical demand and potentially commercial launches. “It allows you to do things at a scale where your capital investment is smaller versus just building a large traditional isolator line that costs three or four times more and has a longer validation and startup timeline.”
Lower Costs Offer Big Advantages For Companies With Early Stage Clinical Drugs
Currently, the BI disposable isolator filling line can produce about 2,000 one-milliliter syringes per hour. This is a large reduction in speed from the traditional filling line; however, if you are not a commercial manufacturing company and you need material from Phase 1 all the way to Phase 3, Greven says the flexibility of the BI filling line allows for them to fill that need. “For a company in startup mode or in initial development for product, it’s uncertain as to what your product's going to do. You don't know if it's going to be approved by the regulatory agencies or not, but you still need to fill it and you still need to get it into clinical trials. Then you still need to ramp it up and get it into the market,” he explains. “This filling line can supply the initial market demand, and then if a company gets approval to do a commercial launch, they can then build that capability and do some things in parallel, dependent upon the clinical trials. The niche we fill is for any clinical material production that a company would need, and we fill it in a manner such that it enables us to do it at a fairly low price point.”
In addition to internal products, BI also has the capability to produce contract manufacturing products for other companies. Instead of going to a larger CMO, the new filling line allows BI to produce the product at a smaller volume, and potentially at a smaller cost, and then the company doesn't have to build that capability in-house.
Dual Purpose Filling Line Reduces The Need To “Get It Right” The First Time
With a growing demand from regulatory agencies to utilize isolator technology, BI’s isolator filling line offers compliance in a flexible manner that enables a company to move with the market as a product gets approved or doesn’t get approved. If there is a problem, the isolator filling line also allows you to fill other types of products, including toxins. “I think it just really broadens your capabilities as a filling site,” says Greven. “With a traditional filling site, you usually build it for a specific type of either vial size or product or syringe format, and that's all the flexibility you have. If something happens in your product portfolio and you don't move forward with that product, then you're stranded with this investment.” In addition, if you have your number one product in a syringe format but then experience difficulties with the clinical trial that don’t allow it to move forward but you have something in the vial format, then you can still do one investment for your isolator line and still have flexibility to introduce vials.
So what challenges does the BI isolator filling line face? “One of the main hurdles is just understanding how to bring in components that are ready to use,” says Greven. “Being state of the art is great. Being one of the first in the market with the flexible isolator filling lines is also great. Unfortunately, what we've encountered is items like ready-to-use vials really aren't used out on the market right now.” Greven says BI is currently navigating a path of understanding about how to bring in ready-to-use components in an aseptic manner. And because the system is being used in a different manner, they can't leverage what the industry has done in the past. For this, Greven says BI, Bausch and Stroebel, and BI’s suppliers are learning together, and in the process, defining how it’s done.